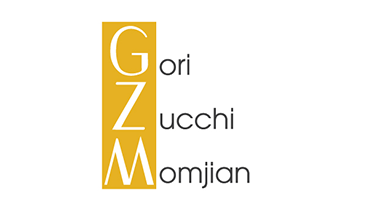
GZM GOLD MANUFACTURING
GZM deploys Microsoft Dynamics 365 Business Central ERP software with the BCGold vertical to manage sales orders, planning and production launches.
About us
GZM is a company specializing in the design and manufacturing of jewelry. In particular it deals with costume jewelry: pendants, rings, bracelets, earrings. The production process is totally covered from the melting to the finished product. The main market is third party business from which is commissioned the production and often the design of the product.
For GZM the control and the quality of the product are fundamental to reach the goal of customer satisfaction. The production process requires a strict control of the precious metal, of the drops in order to have complete control of the metal. In addition, the product is controlled in several stages to meet strict quality standards.
Requirements
The quality standards, as well as the nature of the product, require you to manage production at every stage, track the materials used, and identify shrinkage and the areas where it most affects you. In addition, it is essential to perform various quality checks for the operations performed.
Planning and launching of production is a very important point to ensure compliance with the required deliveries and avoid any delays. Preparation and management of shipments, management of packaging, packing list and customs documents are essential in the final part of the process.
The solution
Dynamics 365 Business Central and the BCGold vertical are the solutions adopted to cover 100% of the customer's requirements. The management of sales orders, planning and production launching guarantee the respect of delivery times.
The management of the movement of valuables, with a strict system of controls and authorizations on all the exceptions detected, allows to know exactly the position of the valuables, moreover every unexpected event is identified and reported to the responsible body. For the phases in which it is necessary, a customizable system of quality controls allows to avoid the introduction in the production chain of products with characteristics not compatible with the requests.
The preparation of shipping and packing lists has been automated, drastically reducing the time spent.
Integration with the Office 365 range of products has made it possible to manage automatic internal alerts or personalized message sending to partners, staff and customers (Outlook and Word among all); as well as in-depth analysis of production data (Excel).
Client Information
- Industry
- Precious metals and jewelry
Benefits
Controlling the process at every point, speeding up the necessary controls and data entry, automating repetitive phases and eliminating external operations have placed the ERP at the center of the system, thus achieving a significant reduction in time and the possibility of expanding the company's objectives.
- Greater precision and speed of response to the customer both in the pre-sales phases, through a streamlined system of drafting the offer, and in post-sales through the optimization of customer service processes (tickets)
- Metal and precious metals control
- Identification of shrinkage in departments
- Identification of products outside specified tolerances
- Recovery management
- Management of exceptions/priorities ensuring rapid response and reorganization of phases
- Faster response to customer requests and continuous process optimization
The Microsoft product we have implemented and the assistance and support we are receiving from EOS Solutions is impeccable! We are very pleased to have embarked on this initially difficult and exhausting path with a company of professionals of the highest level!
The EOS team has always been on hand, providing quick responses and interventions. I highly recommend EOS Solutions to any company that wants to implement a ERP system.